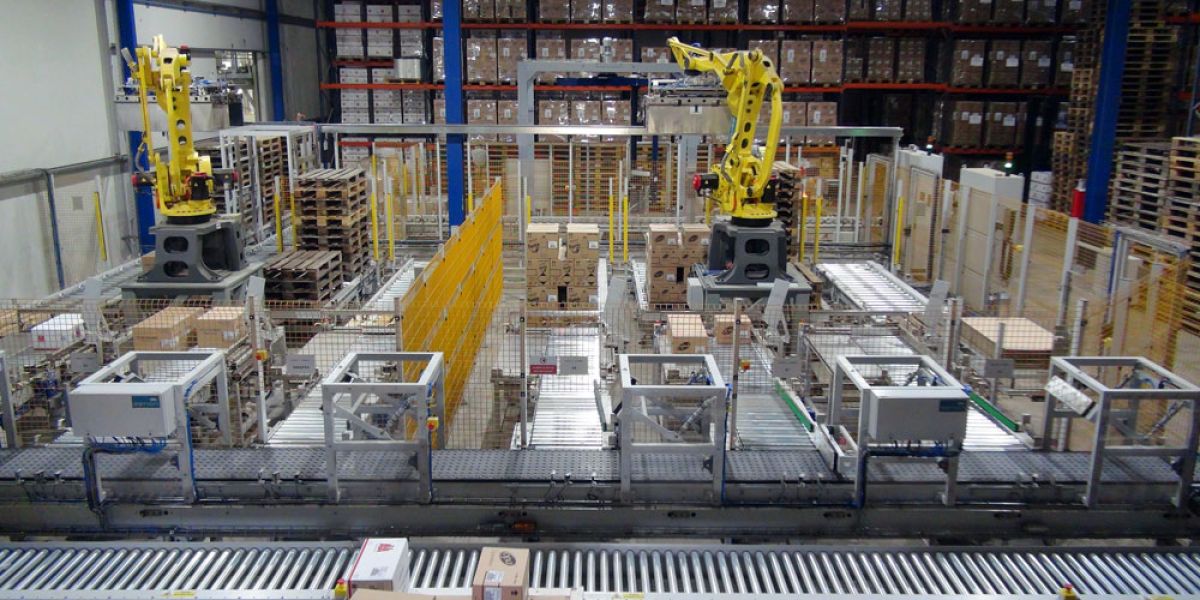
The Need
EUROCHARTIKI SA wanted to automate the End-of-Line of its production process for its six distinct liquid detergent production lines at its premises and to transfer the palletizing processes from production area, where it was manually done, in the warehouse area, with all the advantages that this entails, for raw materials handling and for finished pallets handling and storing.
The Solution
At the secondary packaging level, the investment is about fully automating the case packing processes for its two fastest production lines, and semi-automating of the rest. The goal is to fully automate all lines in the years to come.
At tertiary packaging level, the goal was to gather all the production lines on a central palletizing system per line of origin.
In order to achieve the goal of transferring the palletizing processes from the production area to the warehouse area, the six individual lines are merged into one, which transports them all together to the warehouse area.
The boxes are then sorted based on source line, are being palletized into six distinct palletizing positions, before they are driven to a stretch wrapping machine to stabilize them, then to a print and apply system to mark them with a label and finally to the warehouse.
In more details
Each line is initially automated by a case packing system that takes over the carton forming, product group formation, carton packing and closing of the carton. The carton is then being checked for under weighing.
A print & apply system automatically put two labels in each carton, on the front and on the side, and their correct affixing is checked before the carton is driven to a lift that lifts them to a higher level. The aim is to keep the floor passes clear and not affect the ergonomics of the production area.
After the cartons that are produced by each line are lifted to the higher level of about 3.5 meters from the ground, they are merged into a central line until they reach the warehouse area. There, a spiral conveyor device returns them to the ground level and after they are separated, they are led to a barcode identification system and are being classified into six individual exits.
Each exit has its own automation for grouping the cartons according to the pallet pattern of each production line.
Two robotic arms, three degrees of freedom each, are responsible for the palletizing by taking preformed carton sets and placing them on pallets in six distinct palletizing positions.
Beyond palletizing, automatic is also the empty pallets managing process and the interlayers, the cartons that are being entered between pallet floors to stabilize them. Both consumables are stacked into the system.
In a typical palletizing cycle, the robotic arm receives a pallet from the stack, puts it in the pallet position, then places the stacked cartons on the pallet, and cardboard between the layers whenever required.
When a pallet is complete it goes to a standby position. A pallet transport wagon that unifies the six palletizing positions, leads the pallets to a rotating arm type automatic stretch wrapping machine. Ready pallets are driven, prior to moving away from the system, to a print & apply system, where labels are being printed and applied on the pallets, so that they can be easily identified and handled both in the warehouse and thereafter.
To manage the labels of the six individual carton printing and labeling systems and the pallet label print and apply system, there is a central management system, the Markem’s COLOS, which controls the seven individual systems and sends to each one the necessary static and dynamic information.
The Benefits
The benefits for Eurochart SA from the installation of the system implemented by Zenon are:
- The operating costs of boxing and palletizing have been minimized due to their full automation.
- More flexibility was given in production management and programming, allowing for rapid switching and easy adaptation of the production processes to small productions and eventually to emerging production needs.
- Moving the process of creating a pallet from the production area to the warehouse has left free space, which has helped to keep the plant running more efficiently.
- The transfer of the palletizing process to the warehouse facilitated the management of finished pallets to their storage shelves and minimized the movement of forklifts in the production area, which resulted in improved safety and ergonomics.
- Automation of case packing and palletizing have also lead to significant benefits for the quality of the finished product as it is clearly improved compared to that what was made by hand.
- Automatic labelling and marking and weight control also contributed significantly to better quality.
Click on the photographs for a larger view:
If you are interested in a similar solution, please call us on tel. +30 210 6690900 or fill out the contact form below.
Paper & Products