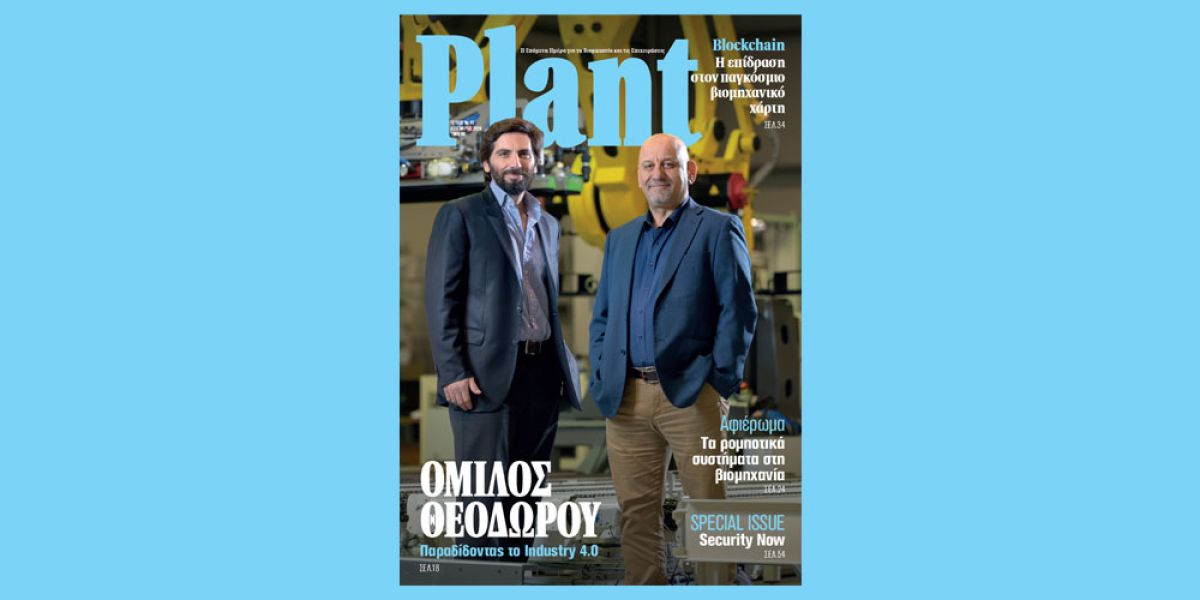
George Panatzopoulos
Plant Magazine Journalist
Theodorou Group: “Delivering the Connected Factory”
With the unshakable belief that through their digital transformation companies gain a competitive advantage, which comes from the deep knowledge of the subject and the continuous investment in innovation, Theodorou Group continues consistently for 35 years to offer solutions that contribute to the integrated automation of production processes and the supply chain. The CEO Evangelos Theodorou and senior executives of the group analyze all these solutions, which can benefit companies, in order not to miss the opportunity of industry 4.0.
To begin, I would like you to tell me what are the solutions offered by Theodorou Group and what are its competitive advantages?
EVANGELOS THEODOROU: Our solutions fall into the following product categories: Robotic packaging, product coding, labeling systems, warehouse automation, product packaging quality control devices, packaging consumables, production management / improvement systems and integrated traceability systems. All our applications are designed with special care, to meet both the immediate and future needs of our customers. We are constantly investing in our staff and we already have 80 specialized technicians. We place special emphasis on after-sales technical support and have seven technical support points throughout Greece so that we can literally always be by our customers’ side.
What is the vision of Theodorou Group?
ET: Our vision is the development of integrated solutions that contribute to the full automation of production processes and the supply chain, through their digital transformation. We strive on a daily basis to prove to our customers that we are not only suppliers of equipment and services, but also their reliable consultants for their digital transformation. We believe that only through their digital transformation will companies be able to gain, not only a competitive advantage, but also to develop new products that will shape new consumer habits.
How feasible is it for industries to adapt to digital transformation and rapid technological advances?
ET: The adaptation of industrial enterprises to the digital transformation requires a change in the way business operations are handled. Many parts of the business, such as production, technical management, IT, supply chain, procurement, quality control must learn to work closely together. It is important that in our meetings with customers, most of these departments sit at the same table with us. For us, this is the signal we are getting that the business is in a real mood to enter a phase of change.
How did you deal with the challenges of this particular year?
ET: In 2020, we completed 25 robotics installations and 16 complex integrated automation / traceability / production management installations in the food, beverage, pharmaceutical, chemical and tobacco industries. We are really proud of the fact that the above facilities were made not only in large, but also in smaller Greek industries. This means that we have the ability to help the entire Greek industry.
What is the strategic plan of the Group in strengthening its export activity?
ET: We started exporting in 2012 mainly in our packaging consumables and continued with integrated robotic packaging and digital transformation systems.
Currently 16% of our turnover is exports and we have regular customers in 25 countries, from England to Saudi Arabia and from Vietnam to Portugal. In England, we founded a local company ENDOLINE ROBOTICS LTD.
What does a system integrator do and what is the relevant role of Theodorou Group?
ET: A system integrator undertakes complex projects and delivers them turnkey. Projects in digital transformation require deep knowledge in many technologies, such as mechanical, electrical, electronic, IT, telecommunications and automation. In our group we have engineers with great experience in all these fields.
We found the pack-experts in your consulting services. Can you tell us a little about it?
ET: We have created a special team of engineering consultants, which we named pack-experts. Typical projects of the group are the studies for the improvement of existing production lines, their extensions for the production of new products, the installation of new production lines, and even the design of new factory premises. Our clients have already enthusiastically accepted the availability of this important consulting service.
Technologies are evolving very fast as opposed to central plan which has to change at a much slower pace. No business wants to have equipment that does not meet its current needs. How does servitization solve this problem and what is its dynamics?
ET: Servitization enables the use of equipment in the form of high value-added services. When the equipment can no longer meet the needs of the company, it is replaced with new equipment. At the same time, the old equipment can be used by another company, which is in a previous stage of transformation. Our Group has started Servitization since 1997 and it has now been proven that in addition to the many advantages, Servitization offers a cost reduction of at least 30%.
What are the innovative robotic systems you have installed in the packaging sector?
ANTONIS ALEXANDROPOULOS: It is our strategic choice to develop innovative products and this has entered our culture and philosophy. So in the field of robotics, we went beyond the logic of developing classic autonomous systems and proceeded to innovate their integration into the interconnected systems of the factory. Many years before the advent of the fourth industrial revolution (Industry 4.0) we developed solutions, which fit exactly into this logic, robotic palletizing and case packing systems, which are interconnected with central software (ERP, MES, etc.), with which exchange data automatically. That is why we are not only able to claim that our systems are ready to be part of the industry ‘s digital transformation program, but in many cases these are the core on which it is based to evolve. Interface is what offers tremendous flexibility and simplification in the use of otherwise robotic systems, further cost reduction, absolute reliability and transparency.
What are the new methods and technologies in the various stages of pallet shaping?
MARIOS HADJIANDREOU: Robots are an important pillar of the digital factory, and they are becoming more and more intelligent with more flexibility and interconnection capabilities. For example, they can undertake the construction of a pallet from many different products (mixed pallet), while they can also be used as part of an automated pallet aggregation process for Track & Trace purposes. At the same time that robots are becoming smarter, costs have been significantly reduced, and standard modules are available. Our company has developed PalletMat – Plug & Play Palletizer in a Cell, which cover a range of palletizing applications (cartons, bags, multipacks, etc.), while at the same time they can be easily moved to another area of the factory, thus serving more lines or needs, existing or future. Standardization achieves greater economy and now robotics can benefit “smaller” companies.
How do the robotic solutions you offer help automate product case packing?
MH: We have developed a series of solutions for automatic grouping and placement of products in boxes, paying special attention to the rate of production, quick and easy product changes, but also to the flexibility and scalability of the system. Especially for widespread packaging such as pet bottles, aerosols, flat bottoms or pillow bags, we have developed the standard CartonMat systems, which undertake the configuration of the box, the grouping / placement of products, but also the closing with tape or glue. In the last year we have completed important projects in Greece in large companies of chemicals, cosmetics, coffee, etc., while the CartonMat series is also available through our network of representatives in Europe.
What are the robotic systems you provide that contribute to warehouse automation?
MH: I would like to refer to two conditions, which pushed in the past and are now pushing warehouses to intensify their automation efforts. The first was the financial crisis that drastically changed the distribution of medicines with pharmacies on the one hand placing smaller orders, but much more often, and on the other hand the drugstores having to execute them immediately with much higher management costs. The only way out was integrated automation, from receiving the order to packaging and shipping. Our company has developed a fully automated Order Execution robotic system and we have implemented important projects in this field. We are seeing something similar now with the new treaty being created in the C-19 era and the launch of e-commerce. The difference is that automation is now becoming an imperative in all warehouses, from couriers to supermarkets. Our systems fully automate the processes of picking, packing, sorting, while the new generation of cooperative robots can work harmoniously with humans in the same space, increasing the overall efficiency of the warehouse.
How long does it take for an industrial enterprise to recoup an investment in robotic systems?
AA: It is very important to make a thorough analysis of both the current situation and the future plans of each company, on which the study and design of a robotic automation system should be based. The benefits of investing in modern robotics systems are manifold. More specifically, they refer to the drastic reduction of costs, the unquestionable increase of productivity, the improvement of the safety and quality of the produced products and in conclusion, to the improvement of the competitiveness of the company, since a well-designed and designed robotic automation system gives a clear competitive advantage. in business. However, care is needed as the above benefits are not fully guaranteed, unless there is first an in-depth study by an experienced team of highly technical training and specialization. Theodorou Group has invested in a team of engineers, who in collaboration with the company designs the appropriate solution for the current need, but also the future requirements. The depreciation time of such a system also depends on the above approach, which, in many cases, can be even less than 24 months.
What are the benefits that users can get from the Modular End of Line (MEL) system and what are its installation phases?
AA: MEL System® (Modular End-of-Line) is a real development in the design and implementation of integrated End-of-Line systems. It incorporates two very important innovations: A modular approach to the integration of mechanical equipment (the general idea of MEL-ready modules) and the backbone, an ultimate control and IT system that combines Industry 4.0 technologies (MES, PLC and SCADA). An additional advantage of the system is that it can integrate supply chain functionality (eg automated direct shipment and warehouse tracking). Since MEL System® is a integrated system that covers all the productive needs in the packaging process, it is divided into four autonomous and distinct implementation phases, so that there is the optimal adaptation and integration to the needs (present and future) of the company. These phases are distinguished depending on the phase of the package and so we talk about:
- ΡΡΟ Phase (Primary Packaging Operations) which includes coding, weight control, labeling, quality control and sorting solutions.
- SΡΟ Phase (Secondary Packaging Operations) which includes solutions for shaping and closing cartons, boxing, coding, weight control, labeling, quality control and sorting.
- ΤΡΟ Phase (Tertiary Packaging Operations) which includes palletizing solutions, pallet wrapping with stretch film and pallet coding according to GS1.
- DS/DW Phase (Direct Shipping/Delivery to Warehouse) which includes solutions where pallets are delivered either directly for loading or in storage.
MEL System® has been successfully installed in numerous multinational industrial companies, achieving a significant increase in productivity, AIF and the optimal utilization of existing infrastructure.
In what areas of industrial production can cooperative robots be used? What technological solutions have you developed in this area?
MH: Cobots work with humans in a common workplace to perform various repetitive tasks, such as packaging (case packing, palletizing, etc.), quality control, machine operation, product picking and sorting. The installation of such a system is very fast, while it can work almost anywhere, covering future needs of the company. Of course, cobots at this stage can not completely replace industrial robots, which are much larger in capacity. The category of collaborative robots also includes autonomous mobile robots that move intelligently in space, transporting materials from one place to another (eg, feeding machines with raw materials, transporting ready for storage), freeing valuable time from employees. It is important to mention that the coexistence of robot and human has a positive sign in the performance of the employee himself.
How do you envision the future of robotic systems and what are the strategies you will devise in Greece and abroad?
MH: First of all, market trends and consumer habits are changing faster than technology itself, especially in conditions like the ones we live in now. So the most important thing is not the technology itself, but the ability and the mood of the business to change. Of course, technology is evolving and the only sure thing is that robotic systems will be able, not just to perform predetermined repetitive tasks, but to make and implement decisions and be trained. The degree of human interaction in the same space is increasing and many have already started talking about Industry 5.0, where man returns to the factory, but not as a unit of work but as a governing body. For our part, we take care of all the systems we design to offer a high degree of flexibility and scalability, while standardization helps us to offer solutions in the form of value-added services, thus reducing the risk of investment for our customer.
Serialization & Aggregation, Integrated Packaging Systems, Connected Automation Systems